MarkBarbieri
Semi-retired
- Joined
- Aug 20, 2006
Have any of you made dye sublimation prints onto Aluminum? My wife and I were volunteering at an art festival last weekend and saw some really amazing looking prints on metal. I talked to the artist for a while and he explained that he made his with a dye sublimation printer onto specially coated aluminum. We have a dye sub printer at my wife's maker space, but I've only used it for things like fabric bags, mugs, and stuff like that. I've never tried to make real prints of pictures with it.
I ordered 8 cheap 8"x6" aluminum sheets and they arrived today. I'm going to go in tomorrow and try making some prints to see how the colors and tones come out. I tried finding some ICC profiles for the aluminum, but I couldn't find anything. We'll see how it goes without profiling. I think my printer profiler is so old that it is no longer supported and I'd really prefer not to buy a new one.
Here are the prints I think I'm going to start with. I wanted things that are very saturated, some human faces, at least one with a very a large monochromatic area, and lots of different colors.
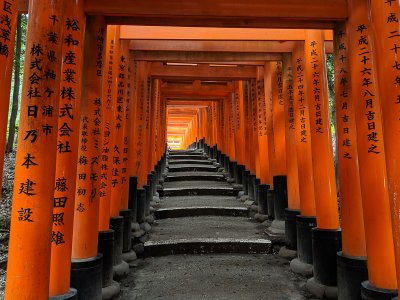
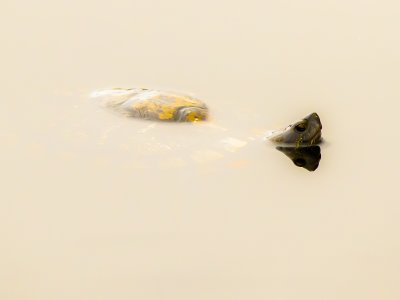
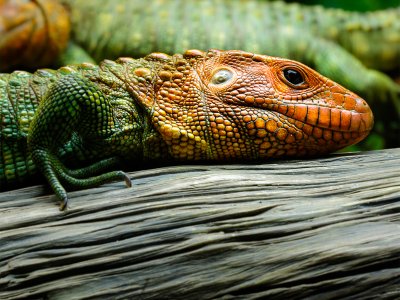
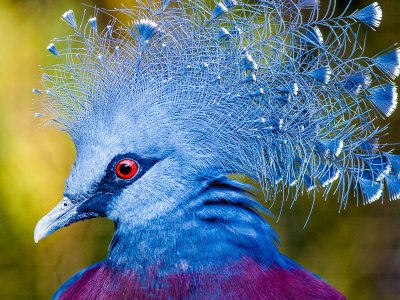
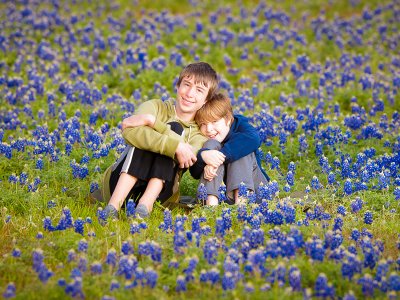
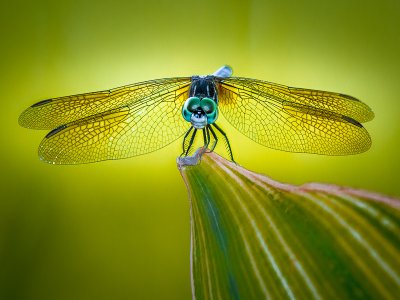

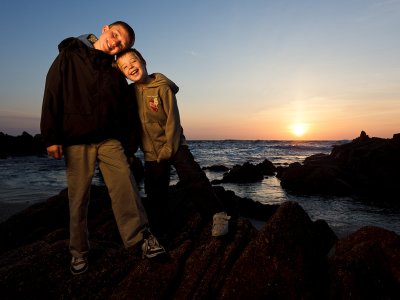
I ordered 8 cheap 8"x6" aluminum sheets and they arrived today. I'm going to go in tomorrow and try making some prints to see how the colors and tones come out. I tried finding some ICC profiles for the aluminum, but I couldn't find anything. We'll see how it goes without profiling. I think my printer profiler is so old that it is no longer supported and I'd really prefer not to buy a new one.
Here are the prints I think I'm going to start with. I wanted things that are very saturated, some human faces, at least one with a very a large monochromatic area, and lots of different colors.
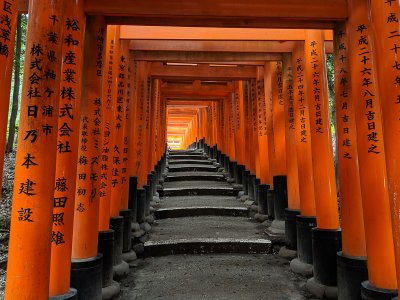
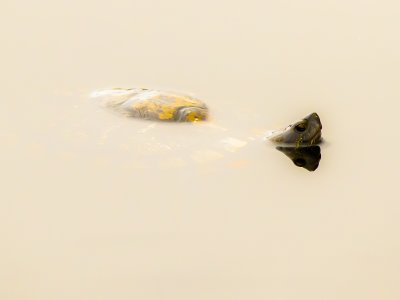
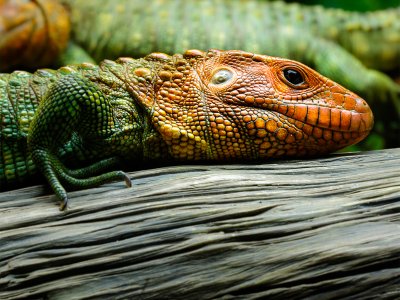
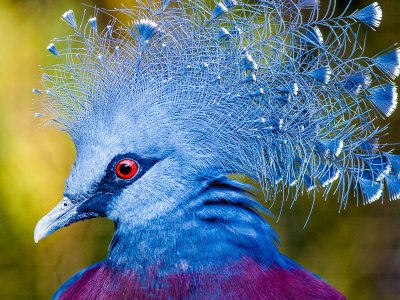
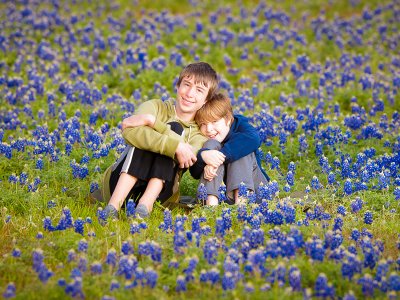
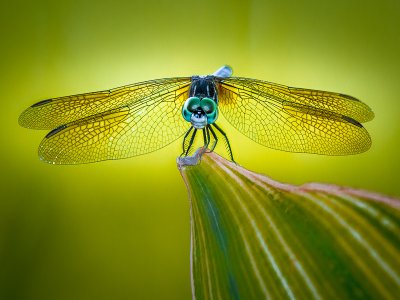

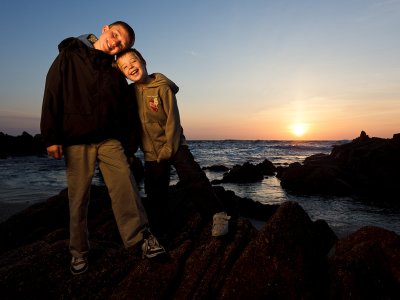